25 MWs thru solar
& cogeneration
Millions of gallons
wastewater cleaned
100% solar powered
HQ & yard
LEED & SWPPP
Certified Staff
Our Responsibility
As general contractors, our actions and decisions have a big impact on both our local community and the environment. We are committed to integrating sustainability practices into our everyday operations, material sourcing, design approaches, and construction techniques.
Our Biggest Impact:
Recommending lower carbon building materials
We work with our engineers and suppliers to optimize concrete mix designs to contain higher percentages of low carbon admixtures in lieu of cement. We can often achieve 30% reduction in concrete carbon emissions on a project by optimizing the specified concrete. Since concrete related activities make up 55% of our work volume, these savings can add up.
Fly ash, slag and other admixtures, known as Supplementary Cementitious Materials (SCMs) can replace some of the Portland cement in concrete without affecting cost, strength or durability. These admixtures are byproducts of industrial processing. Slag happens when iron ore is melted and fly ash, a rough textured particle, is a remnant of burning coal. Using these byproducts in concrete provides circular benefits for industrial processes while at the same time lowering the embodied carbon in concrete.
Low carbon concrete is suitable for foundations, slabs, pavements, and wall applications. Even tilt-up wall panels can be constructed with low carbon concrete mix designs. There is no material cost increase to use low carbon concrete, but cure times usually increase, so schedule needs to be carefully considered.
The only application not suitable for SMCs is pervious concrete, such as site paving that needs to allow rain to permeate into ground waters.
Finding structural approaches to reduce carbon
The most significant scope for reduction in building mass is often found in structural design.
- For example, Overaa works closely with our structural design partners on certain projects to reduce slab or beam span (and increase associated column density) which can yield carbon savings.
- Alternatively, we recommend technologies such as mass timber in lieu of concrete or steel structural members to achieve significant carbon savings.
- For example, for the Michelle Obama School in Richmond, CA., we used long spam Glu-Laminated Timber (GLT or glulam) and Structural Composite Lumber (e.g. LVL and LSL) to optimize passive strategies for daylighting and reduce construction costs.
Finding construction efficiencies
- Prefabrication can decrease waste and improve schedules, but must be carefully weighed against transportation costs.
- Centralization of various tasks, such as preassembling wall components in a controlled environment, can streamline operations and reduce waste.
Aggressive material waste management
- We actively promote an internal “buy back” program to incentivize re-use/recycled material.
- Reducing material waste with thoughtful, site specific landfill diversion programs.
- Increasing material reuse by purchasing materials, such as concrete forming materials, that can be reused for several applications.
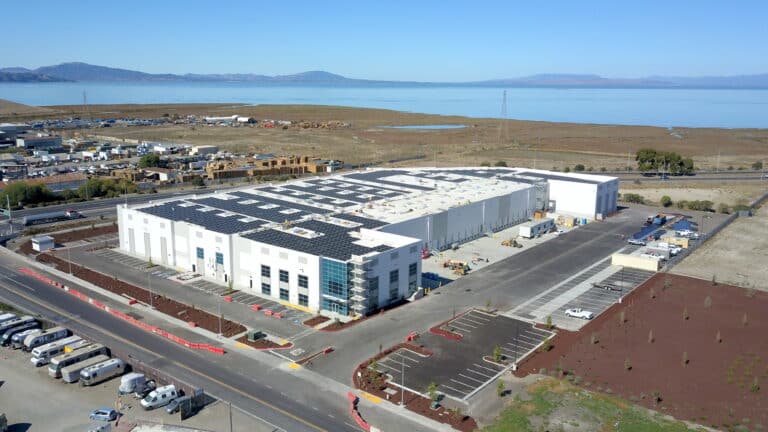
Sustainable Development Strategy
For every project, our goal is to decrease embodied carbon emissions through strategic material selections and construction processes. Embodied carbon is the amount of carbon emitted into the environment from a building during its entire lifecycle: manufacturing, installation, construction, maintenance, and demolition. (Embodied carbon is different from Operational Carbon, which measures building energy consumption.) When choosing various construction materials, we consider its lifespan, including extraction, transportation, construction and disposal.
California building codes as of July 1, 2024 specifically aim to reduce embodied carbon emissions in the construction, renovation or adaptive reuse of commercial buildings larger than 100,000 SF and schools over 50,000 SF. This reduction can be achieved in one of three ways: 1) Reuse at least 45% of an existing structure 2) Use materials that meet specified emission limits (like concrete with fly ash, slag, or calcined clays and stay away from materials such as foam insulation, aluminum and plastic) and 3) track Whole Building Life Cycle Assessment (WBLCA), a process that documents material type, weight, production process, distance travelled, etc. to calculate expected embodied and operational carbon produced during the lifespan of the building.
During our collaborative preconstruction sessions, we analyze design and construction approaches and offer carbon reduction strategies. We have found that the most significant opportunity for carbon reduction lies in the structural design – specifically the type of concrete we use and the approach to framing. On past projects, our deep understanding of the nuances of these building materials and methods has enabled our clients and design teams to make informed decisions, and has resulted in substantial carbon savings.
During the construction phase, we focus on reducing material waste, finding efficiencies and opportunities for re-use, and sourcing clean energy for operations.
Measuring and understanding the carbon impact of construction is an important step towards carbon neutral construction. Our Environmental Strategy is aimed at assessing our actions via quantifiable metrics, within the following categories:
- Carbon Emissions
- Material Waste Management
- Water Management
- Project Selections & Stewardship
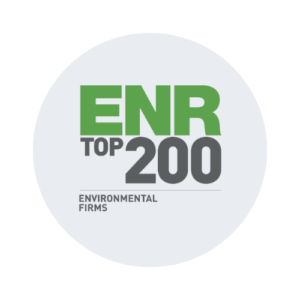
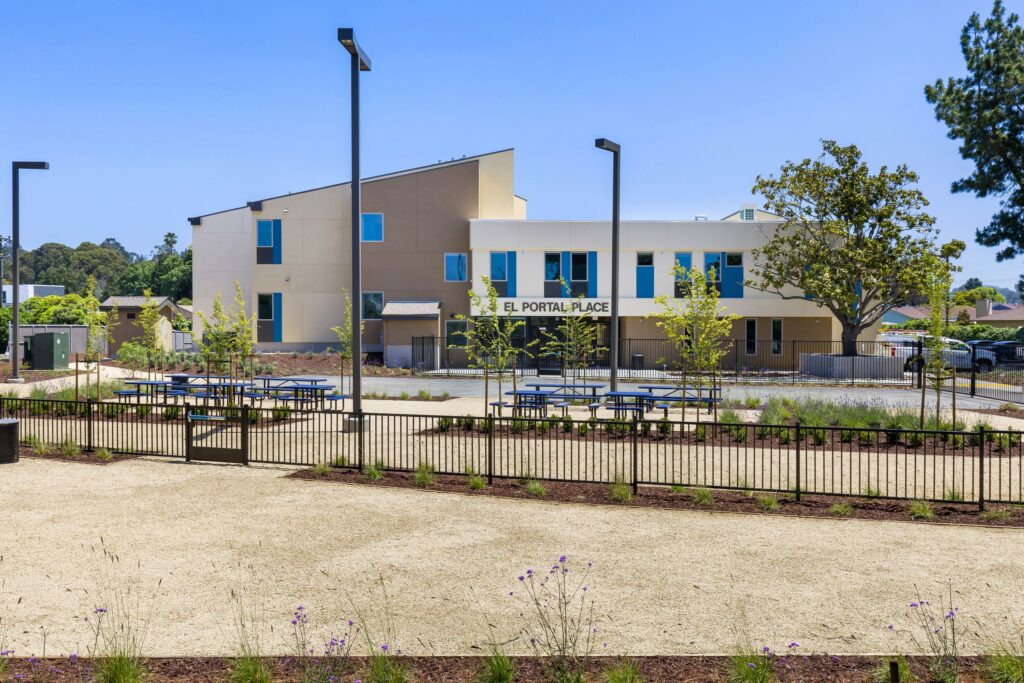
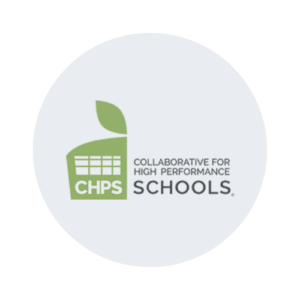
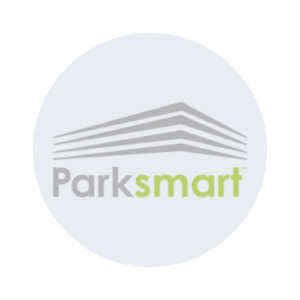
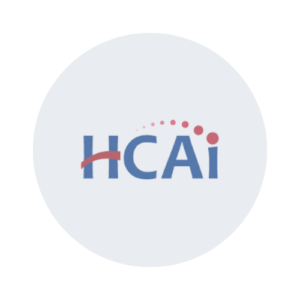
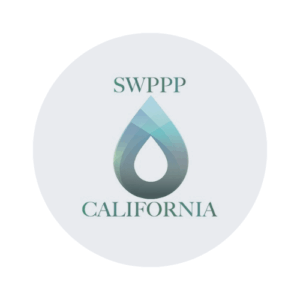
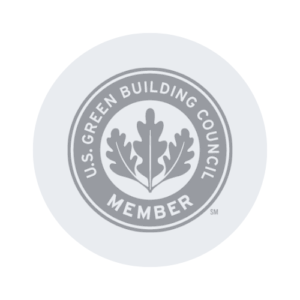
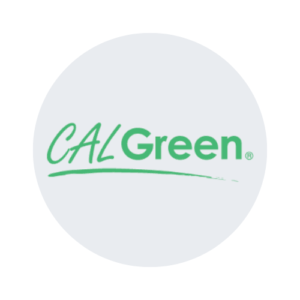
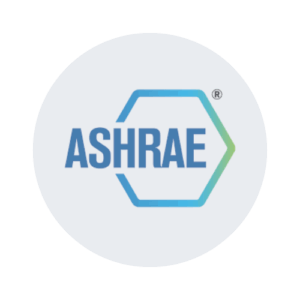
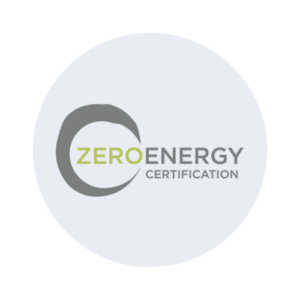
Overaa's Sustainability Goals
LOW CARBON CONCRETE
REDUCING CONSTRUCTION WASTE
Goal 1 | Carbon Emissions
Establish a corporate carbon commitment and metrics.
- Integrate Embodied Carbon Calculator (EC3) and make informed procurement selections based on low carbon emissions.
- Collect Environmental Product Declarations (EPD) for materials used which include a cradle-to-gate Life Cycle Assessment (LCA).
- Partner with suppliers to increase cement replacement alternatives in concrete mixes, and partner with designers to provide lower carbon building alternatives such as mass timber.
- Increase usage of solar power or other renewable energy sources, such as green powered generators at jobsites, prefabrication sites, and offices.
Goal 2 | Material Waste Management
Restructure Waste Management approach for optimized landfill diversion and transparency.
- Reduce total waste generated on jobsites.
- Increase usage of reusable formwork.
- Aggregate forming operations in centralized locations to facilitate reuse.
- Invest in reusable aluminum and steel formwork.
- Increase centralized and prefabrication operations where viable.
- Increase number of projects certified with TRUE Zero Waste program. (Certified projects divert 90% from landfill.)
- Utilize Recycling Certification Institute (RCI) facilities for mixed construction and demolition.
Goal 3 | Water Management
Reduce virtual water consumption (water consumed during construction projects) and protect groundwater and runoff from contaminants during construction activities.
- Provide SWPPP (Storm Water Pollution Protection Plan) leadership on every project.
- Increase usage of rainwater harvesting, greywater recycling systems.
- Use water metering through smart irrigation systems, pressure-reducing valves.
- Use water-efficient toilets.
- Decrease usage of plastic single use drinking water bottles on construction sites.
Goal 4 | Project Selection & Stewardship
Seek projects that help the environment and align with partners that share our values. Be proud of the legacy we create.
- Pursue local projects near our workforce.
- Seek out water purification, water recycling, material recycling, and green energy generation projects such as solar, cogeneration, hydrogen, and biofuel.
- Seek out LEED projects, ParkSmart projects, and other certified green building projects.